A few questions- wanting to sell a headjoint
23:05 on Saturday, January 31, 2009
|
|
|
Re: A few questions- wanting to sell a headjoint
05:59 on Sunday, February 1, 2009
|
|
|
Re: A few questions- wanting to sell a headjoint
12:18 on Wednesday, February 25, 2009
|
|
|
Re: A few questions- wanting to sell a headjoint
19:58 on Wednesday, February 25, 2009
|
|
|
Re: A few questions- wanting to sell a headjoint
20:35 on Wednesday, February 25, 2009
|
|
|
Re: A few questions- wanting to sell a headjoint
12:57 on Thursday, February 26, 2009
|
|
 |
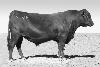 Tibbiecow (480 points)
|
OK, I'd price a used headjoint in excellent condition at slightly above half retail, new.
That's the price I've paid for most of mine- I bought a Miya MZ5, sterling, engraved lipplate for $350 off eBay.
I also just bought an eBay flute, for its head and footjoint- it is a Yam 285S, open holes, inline. It came with a B footjoint, and a handmade sterling Yamaha CF headjoint. I am expecting to sell the HJ for $250 or so; it's in perfect shape and it is very nice to play. (It isn't a CY, the taper is not the same.)
So, anyway, the footjoint will not be used much, but there is some pitting in the finish. Is there a way to make this thing look better, while the mechanism is off for repairs/adjustment/padding?
|
|
 |
|
Re: A few questions- wanting to sell a headjoint
14:06 on Thursday, February 26, 2009
|
|
|
Re: A few questions- wanting to sell a headjoint
20:44 on Thursday, February 26, 2009
|
|
|
Re: A few questions- wanting to sell a headjoint
07:03 on Friday, February 27, 2009
|
|
|
Re: A few questions- wanting to sell a headjoint
12:43 on Friday, February 27, 2009
|
|
|
Re: A few questions- wanting to sell a headjoint
03:55 on Saturday, February 28, 2009
|
|
|
|