Re: Going to try to repad a flute..
Re: Going to try to repad a flute..
18:37 on Wednesday, September 1, 2010
|
|
 |
 jim22 (247 points)
|
So, I've completed "flutes 101" and done a little work in the field. Professor Micron teaches the PhD students. Maybe I can TA for him  - I'm sure I will learn a great deal.
Let's not forget that EVERY tech who has done 6 flutes, 20 flutes, or a few hundred flutes at one point in time did his or her 1st one. I say go for it! I have found it very rewarding so far. There is no shortage of flutes to revive on eBay that should otherwise go in the dumpster. One of my favorites is an open-hole emerson that the plating is falling off the body, but it plays great! It cost me $11 US and about that much again for shipping.
I'll be lurking about to be as helpful if I can. Micron (and the other techs), please keep an eye on me so I don't mislead (thanks!). -- Jim
|
|
 |
|
Re: Going to try to repad a flute..
11:15 on Friday, September 3, 2010
|
|
|
Re: Going to try to repad a flute..
12:29 on Friday, September 3, 2010
|
|
|
Re: Going to try to repad a flute..
12:40 on Friday, September 3, 2010
|
|
|
Re: Going to try to repad a flute..
14:54 on Friday, September 3, 2010
|
|
|
Re: Going to try to repad a flute..
11:00 on Saturday, September 4, 2010
|
|
 |
 jim22 (247 points)
|
On feeler gauge making and using...
My latest feeler gauges are made with a length of audio cassette tape glued to a length of bamboo skewer with contact cement. The cassette tape is about .0005" thick, and a little less than an inch past the end of the stick seems about right. You can take the curl out of it by holding it between your thumb and a sharp edge like the side of the tweezers and dragging it across the edge, like the opposite of making curls in ribbons.
Select a pad of the correct diameter - the next size smaller than "too tight to get in and out of the key cup conveniently". Put it in with a couple .008" full shims under it, and then put on the pad retainer or screw/washer. Too many shims and the screw may be difficult to thread in, not catch many threads, and be too tight on the pad causing lots of wrinkles. Too few shims and the screw will bottom out in the spud and will not hold the pad securely against the shims and inside of the key cup. You want to be at a happy medium to start with.
With the pad secured in the key cup, put the key on the instrument. If the thickness is really bad, you will see gaps at the back (hinge side) or front of the cup. If it's close, you may not see the gap, and that's where the feeler gauge comes in. Insert the feeler gauge between the pad and the tonehole at the front, and then at the back. At each position, apply light pressure (much lighter than as if you were actually fingering the key to play the flute) to the key, and pull on the feeler. If there is contact, you will feel a drag as the feeler pulls out. If there's a gap, the feeler will slip out with no resistance at all. You eventually want to do this all around the key at about 8 spots.
In all likely-hood you will find gaps. A gap at the back of the key would be handled by inserting more shims. A gap at the front by removing shims. In a perfect world that would handle all your problems. Flutes are NOT perfect.
It is probable that the number of shims required to get the front-back gaps eliminated may not be within the capabilities of the screws/washers to secure the pads. I handle this by bending the key. One way is to put the key cup in a vise and tap on the key arm at the hinge tube with a very small hammer and wooden dowel as a punch. Need to tap it the correct way, so think about it first! Another way for small adjustments is to put something gentle as a spacer between the pad and tonehole at the front/back where the pad touches and tap down on the back/front where the gap is. To do this on the instrument you must put the flute body on a mandrel. I have found that this can affect neighboring keys. Usually an amazingly light tap is required.
Gaps on the left and right are handled by bending the key. A gemeinhardt I just finished had soft enough metal that I could do this simply by inserting a spacer and pressing down on the opposite side, but the Armstrongs, Artleys, and Emerson I worked on needed the hammer/punch trick. Again, this can affect neighboring keys and can cause trouble with the F# key binding.
That brings us to partial shimming - where you cut sections of shims to close gaps under the pads. This handles a situation where toneholes are not flat/level as is typically the case for student flutes, and also handles variations in pad thickness. Partial shimming is controversial! Some will tell you they are never needed, and every partial shim causes leaks at each end of the shim. They are certainly tedious to design and install. I believe it is possible to use pads which are quite soft, get them as close as possible without partial shims, and then dampen, clamp and heat to handle the rest of the issues, but the pads I have used so far are not soft enough for that. So, I use partial shims.
I use a Sharpie marker to mark gaps on the top of the key, flip the key over and transfer the marks to the rim of the key cup, and finally to a full shim under the key. I mark the full shim at the back of the key and the back of the key cup so I can keep them oriented. I glue partial shims to the full shim. Try not to make "science projects"! To me, this is the part of a repadding job that tries my patience the most.
Deciding what thickness of shims to close gaps must be an experience thing. It seems to me that .001" will make a light spot less light. .004" is a lot for a partial shim but occasionally required to close a large gap, and then be careful to cut the shim about 1/3 smaller than the gap. .002" shims are useful, and if I had .003" available they might be even more useful in closing typical gaps. Micron has insisted shimming is required down to .0005". I have not reached that level of technique yet, but the pads I typically use (MusicMedic) seem forgiving down to about .001".
When I get to the point that the feeler has relatively consistent drag all the way around the key, I dampen the pad surface by inserting a damp paper towel and holding the key closed on it for 10 seconds, then hold the key closed with moderate finger pressure (just a little tighter than actually playing) and heat the key with a hair dryer until I burn my fingers  . Then blow cool air for a minute or two. When you release the pressure you should see a very light impression of the tonehole all the way around the pad. Again, this is how it works with the MusicMedic pads. The Votawtool Prestini Medium pads may take a little less of a tonehole impression and may need a little more precise shimming first.
(Micron - How'd I do?  )
|
|
 |
|
Re: Going to try to repad a flute..
12:48 on Saturday, September 4, 2010
|
|
 |
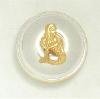 musicman_944 (257 points)
|
Jim has given a very respectable description of using the feeler and shimming, however, I'll add a couple of points. After you initially install the pad the first time, you should mark the pad orientation. Pads are seldom perfectly uniform in thickness around all 360°. When you remove a pad to add or remove shims, you should be absolutely sure that the pad is put back with the same radial alignment. Otherwise, a tedious and frustrating job becomes more difficult. I use a soft (#2) pencil (not too sharp to avoid tearing the pad skin) and lightly mark the edge of the pad at the center of the key arm. When I put the pad back, I align the mark with the center of the key arm to keep the same radial alignment. If you don't do this and a pad has variations in thickness around its circumference, the high and low spots will move and that will negate much of your work locating those spots making your job more difficult.
Also, I try to avoid bending keys unless it is obvious that the key is not level with the tonehole. Sometimes it is unavoidable, but for me, I only do it when absolutely necessary to get good alignment.
|
|
 |
|
Re: Going to try to repad a flute..
19:13 on Saturday, September 4, 2010
|
|
|
Re: Going to try to repad a flute..
19:18 on Saturday, September 4, 2010
|
|
|
Re: Going to try to repad a flute..
19:44 on Saturday, September 4, 2010
|
|
 |
 jim22 (247 points)
|
The music medic pads are nice for the price but the skins are too tight creating a domed surface. |
|
JD, it sounds like you have some interesting insight. I wonder if the "domed surface" is related to some of the issues I've had with pads not fitting under the retaining screws and washers. What issues do you think it would cause? Do you know who manufactures these pads and if they are a MusicMedic exclusive? Unfortunately, one size I ordered is on back-order again, which makes it hard to finish instruments needing the back-ordered size. It took many months to get 11.5mm pads last time they were backordered. This time it's 18.0's.
I too prick holes in the small pads, usually four holes on the sides of the pad spaced around the diameter. I tend to use a minimum of glue pellets under the pads, not wanting it to ooze out when I set the pad into the cup. I'm not sure I'm using enough glue. I suppose I should pull a pad back out and see what coverage I'm getting.
|
|
 |
|
Re: Going to try to repad a flute..
13:40 on Sunday, September 5, 2010
|
|
 |
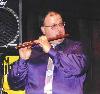 JButky (657 points)
|
I wonder if the "domed surface" is related to some of the issues I've had with pads not fitting under the retaining screws and washers. What issues do you think it would cause? |
|
The "domed pad" effect you might be referring too might also be the pad backer sitting on top of the pad nut. Some flutes have this and need a larger hole cut out in the back cardboard so they don't dome and sit funny in the cup. The opposite problem is the "dished" pad where the pad is too thick for the key cup and/or over-shimmed..
I too prick holes in the small pads, usually four holes on the sides of the pad spaced around the diameter. I tend to use a minimum of glue pellets under the pads, not wanting it to ooze out when I set the pad into the cup. I'm not sure I'm using enough glue. I suppose I should pull a pad back out and see what coverage I'm getting. |
|
4 holes is excessive. One is sufficient. When you glue is soft rotate the pad 45 degrees with a little finger pressure and twist to insure your glue coverage.
Joe B
|
|
 |
|
Re: Going to try to repad a flute..
13:57 on Sunday, September 5, 2010
|
|
 |
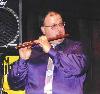 JButky (657 points)
|
Deciding what thickness of shims to close gaps must be an experience thing. It seems to me that .001" will make a light spot less light. .004" is a lot for a partial shim but occasionally required to close a large gap |
|
"If" your washer compression is correct then closing a localized .004 gap means your pad cup angle probably needs correction and/or your tonehole is really bad. There are a number of ways to correct that and you probably need to utilize a few of them to end up with an even job.
The important part when starting out flute padding that people forget (or were never taught) is to consider what affect you are making to the pad itself. While you can be "successful" padding a flute without taking into account what's happening to the pad itself and its operational tolerances, you will have completed a job that does not have the feel that it can have and/or will shorten pad life and stability.
Joe B
|
|
 |
|
Re: Going to try to repad a flute..
21:30 on Sunday, September 5, 2010
|
|
|
Re: Going to try to repad a flute..
17:51 on Monday, September 6, 2010
|
|
|
Re: Going to try to repad a flute..
19:19 on Monday, September 6, 2010
|
|
 |
 jim22 (247 points)
|
do you glue your shims in place? |
|
Yes. There are two possibilities: (1) glue partial shims to a full shim. Mark the full shim with a 12:00 position at the center of the key arm, and build up partial shims on it until the pad fits. As mentioned before, mark the pad similarly and always install the marked full shim and pad in the same orientation to the key arm. (2) glue partial shims to the back of the pad itself. I have been gluing partial shims to a full shim, that way I can always start over if it gets out of control. I have been using an arts and crafts type glue stick (cringe!) to glue the partial shims in.
Putting the flute aside when you get tired or out of patience is a great idea. I find the whole padding task quite iterative, making several passes over the complete flute before I'm really happy with the pads. I'm guessing the professionals are more efficient.
There are 3 "G" keys - the upper and lower inline G keys and the offset G or G# key. The Burkart-Phelan book has the naming convention in it and is very useful. Padding the two inline keys is quite challenging. I've been wondering if there is a systematic approach that should always work, for example:
1. Pick your favorite, upper or lower. Install a pad and full shims that are comfortable. Level the key front-back and/or adjust the full shims. Level the key left-right. Partial shim to achieve enlightenment.
2. Repeat for the other key, with the added challenge that it must meet the tonehole simultaneously.
Step 2 needs more detail I think. The last flute I worked on I tried bending the high key to get coverage, but each time I did, I lost coverage on the first, or created gaps at the back. I'm thinking that when you try to bend a key up or down, really what bends is the cup right at the back at the key arm, so raising or lowering a key really raises or lowers the front, but doesn't really do much to the back. Maybe step 2 should be:
2. Repeat for the other key, with the added challenge that it must meet the tonehole simutaneously at the back and then be leveled front-back.
Just thinking. It really is pretty artsy, a little like sculpture, with a little geometry thrown in. I like it!
|
|
 |
|
|
|
|