Re: Pearl 665 special edition- with Forza headjoint - the right choice ?!!
Re: Pearl 665 special edition- with Forza headjoint - the right choice ?!!
21:13 on Tuesday, December 4, 2012
|
|
|
Re: Pearl 665 special edition- with Forza headjoint - the right choice ?!!
21:26 on Tuesday, December 4, 2012
|
|
|
Re: Pearl 665 special edition- with Forza headjoint - the right choice ?!!
07:46 on Wednesday, December 5, 2012
|
|
|
Re: Pearl 665 special edition- with Forza headjoint - the right choice ?!!
12:45 on Wednesday, December 5, 2012
|
|
 |
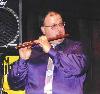 JButky (657 points)
|
Yes, Pearl is the only manufacturer to make a complete line of pinless flutes. Everything from student through pro, harmony flutes and piccolos are all our same basic pinless concept. We were the first to introduce a complete line and still the only. Our pinless is quite simple too, which makes it easy for anyone to work on.
Another question: Isn't a headjoint considered hand-cut if the craftsman uses a scraper to under- and over-cut the embouchure hole? Or is there something more involved with the use of the words "hand-crafted" or "hand-cut"? |
|
Hand cut, handmade, Hand finished are marketing descriptors and don't really speak to the actual manufacturing process. If you want to be really technical, ANY flute, ANY manufacturer is "hand made". Flutes are fairly complex and there are few purely automated steps at the production level. These steps are often used even in pro flutes. Hand cut, hand finished, hand crafted all mean that a craftsman oversees and finishes the final product, be it by scraper or hand control of machine. This is the only way to truly bring consistency to any product. Today, most of the tedious work of rough cutting is done by CNC machine. Then a craftsman does the touch up to the required specs. Could be a scraper, could be a mill, etc, etc..
As quality increases to pro level, the differences are in Quality of materials, Design aspects, and delivering very high levels of manufacturing tolerance. Machines aid a lot towards consistency, but final human touches often make a huge difference.
Here's a picture of a Forza being hand finished at our factory, (just so you can understand easier..)
https://docs.google.com/open?id=0B1SrkrZ7j7Yfdl9reDRPa3lEUmc
Joe B
|
|
 |
|
Re: Pearl 665 special edition- with Forza headjoint - the right choice ?!!
12:52 on Wednesday, December 5, 2012
|
|
 |
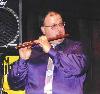 JButky (657 points)
|
Obviously....I am in error - can you please explain what goes on when a technician sits down and goes to work on shaping the embouchure hole. |
|
Production shops use pretty much the same procedure if it is hand cut or handfinished in the Asian shops. Rough cut is done by machine, final cuts are done by a craftsman, Could be a hand scraper, but most likely machine assisted as in the picture.
You are more likely to find completely finished holes cut with scraper only through private individual makers. Again consistency is the issue, there may be a great collection of headjoints but the differences run a wider range. (generally speaking and depending on who the maker is and their individual skill)
Joe B
|
|
 |
|
Re: Pearl 665 special edition- with Forza headjoint - the right choice ?!!
23:03 on Wednesday, December 5, 2012
|
|
|
Re: Pearl 665 special edition- with Forza headjoint - the right choice ?!!
01:12 on Thursday, December 6, 2012
|
|
 |
 Plekto (423 points)
|
I kind of missed the fireworks since I check this site every month or so, as it's kind of slow as of late.
The nitty-gritty of flutes is that the body rarely makes a difference other than options like trill keys, inline vs offset, what type of pads are on it, and so on. But even those are personal preference more than anything.
Why? Because in the end, a flute's body is a metal tube with holes that you plug up in order to make notes. If they didn't play in tune, then nobody would buy them. That is to say, as an example, the body of a basic Powell will sound identical to the body of their top-end model, because, well, it has to in order to function properly.
Not all flutes are made the same, naturally. Pearl, for instance, is made a bit better than Yamaha, IMO. But it's not close to the brute-force approach of a Brannen/Kingma. Of course, it's also a LOT less expensive than a Brannen. But as far as metals, drawn versus regular holes, open vs closed holes, and so on, it's all window dressing that you (often) pay a lot for. And, no, metals make no difference that your audience can actually hear.
So where is the real sound coming from? The player and the head joint for the most part. This is why so many makers are having to also make mid-line models like this. Because tons of players started to do exactly that starting about 20 years or so ago. They would simply get a professional headjoint and keep their old body.
Now you can just buy a flute set up like this. It's really a win-win.
Personally the Forza didn't sound any different than a high-end Yamaha. The Forza is a lot like the handmade EC that Yamaha makes. (which IS a good headjoint, nonetheless. But to be honest, it's a "nice" headjoint. It simply doesn't sing like the better ones Pearl makes.
As for good headjoints without getting into silly money, I personally like the Pearl Calore, the Powell Venti, and the Yamaha K type. If you like the Pearl and can get one of their upper-end headjoints on it instead, consider paying the price difference.
|
|
 |
|
|
|
|